Main Wire Harness Connector

This boating season has started off painfully.1st trip the starter shut us down. 2nd trip, lost my wallet- luckily got it back only missing a $50 Lowe's card (I can live with that, all things considered). 3rd trip (last weekend), hit a stump/log and bent prop (which I bought last year). That gets me to today when the new prop was supposed to arrive, Everything ordered shows up... except the prop. LOL... All the while, the temp gauge hasn't worked- no reading. Worked fine last season, my first owning the boat. So, after a bit of troubleshooting, I traced it to lack of connection passing through the main harness connector. Getting it apart turned into 3 hrs of removing a starter pain all over! It probably took an hour diagnosing and an hour pulling, prying, spraying, and... Ultimately pulled some pins out of both ends of the sockets. 4 were corroded together, the other 5-6 looked perfect. A little di-electric grease at the factory would have saved a few choice words and lots of struggling. It even had the hose clamp on it to seal it. Best I can figure is that a little water was able to follow the wires down through the top of the molded connector.
Word to the wise- pull yours apart and grease it. Di-electric grease every connector you can put your hands on!
So, now the can of worms is open. I assume my best option is to cut out the old connectors and solder in replacements. The boat end won't be bad, but there's not a lot of room to play with on the engine side. I've already got a nice variety of sealing shrink tube, but I need some guidance on the connectors. Are these V-P parts, or common marine parts?
I found a few with Google, but they all seem to say Mercury style. I don't see any "V-P" style. and the Mercury ones appear near identical as far as I can tell. For reference, here's a screenshot I grabbed to be sure what I'm talking about.
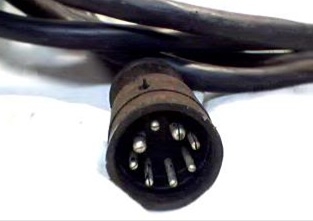
One difference I've noticed is that my engine side has a round flange that's squeezed into place to hold it firm. The "Merc's" appear to have a square flange. This the engine side square- mine is round flange:
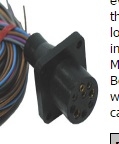
Any expert guidance on this would be greatly appreciated!
Word to the wise- pull yours apart and grease it. Di-electric grease every connector you can put your hands on!
So, now the can of worms is open. I assume my best option is to cut out the old connectors and solder in replacements. The boat end won't be bad, but there's not a lot of room to play with on the engine side. I've already got a nice variety of sealing shrink tube, but I need some guidance on the connectors. Are these V-P parts, or common marine parts?
I found a few with Google, but they all seem to say Mercury style. I don't see any "V-P" style. and the Mercury ones appear near identical as far as I can tell. For reference, here's a screenshot I grabbed to be sure what I'm talking about.
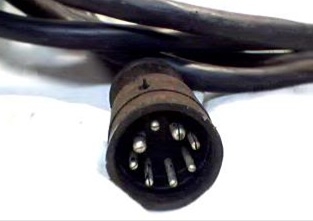
One difference I've noticed is that my engine side has a round flange that's squeezed into place to hold it firm. The "Merc's" appear to have a square flange. This the engine side square- mine is round flange:
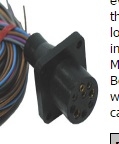
Any expert guidance on this would be greatly appreciated!
Comments
Go figure, they didn't come with screws... At least I can laugh about it!
My curiosity is why are there 2 large pins with heavier wire. I don't see that there are any high current components powered by this harness- all signal wires. I conclude because it's been an industry standard part for many years. That and the current design uses them for indexing the pins. I'm contemplating going with an automotive Delphi connector, but we only have them up to 6 pins here at work.
@NRath, great catch on the pin connector and better attitude. My mother used to say sometimes the only two choices are to laugh or cry so we may as well laugh! Your start to the boating season has been tough by any standard but you seem a lot smarter than average so my money is on you getting that VP all straightened-out!
BTW, great advice on the di-electric. Ford used to insist on putting it into the boots of the spark plug wires for its performance 302s - before pushing them onto the plug tips - better spark, no corrosion and easier to remove the boot wiring harnesses! always had a tube of Motorcraft di-electric around. As you said - wiring connections love the stuff
Nice job!!!
I've got a mixed opinion on that frenchship. I think the vid is making good points on a spark plug boot. It’s one piece with very few points of moisture ingress. Def, it's a non-conductive grease so if it's breaking what would be a connection, no good. The majority of pin and socket connectors aren’t making 100% connection throughout the terminals. There are usually only a few spring loaded points that are actually making contact. In the case of the main harness, I think there are a couple points that run all the way around the sockets for connection. As for DE grease, if not used in excess, my opinion is that the pressure points will displace a reasonable amount allowing for a low resistance connection while filling the voids where air and moisture will sit and start corroding. I can agree that there is potential for it to interfere with a connection, though.
My experience has been ~20 years in powersports- ATV’s and dirtbikes. Mud, dirt, and rain have a way of wrecking things! I’ve never once had an issue with a connection after I started using it. Prior to using it, I cleaned more than one corroded terminal that had shut me down.
Regarding the marine world, I’d say it’s possibly worse than powersports as a covered boat with a little water stuck in the hull is nothing but a condensation chamber. It’s like a breeding ground for corrosion. Pretty much a no win situation!
If you do find yourself with some corroded terminals, I highly recommend a product called De-Oxit. A great product to help a connection. It’s not cheap, but works pretty good. Now, it’s not going to break down 10 yrs of corrosion, but it’s worked well for me on signal wires in automotive where reading resistance is commonplace and precision is imperative.
Corroded terminals inside the motor quick connect. It's not even a waterproof connector! I little work with the file in my multi-tool and we enjoyed the evening on the water. I'll get that connection replaced in the near future.
Go Steelers!!!
Neither Delphi or Ampseal completely ideal, as the heaviest gauge rating is 14. The main harness has either 10 or 12G on the big pins. I didn't have any luck with heavy guage watertight connectors with a little searching. Since there weren't any high current devices on them on my boat, I'm okay with cutting a few strands of wire to get them into the terminals. Then the seal doesn't fit the heavy insulation, so I threw on a couple wraps of electrical tape to fill the small gap between wire and housing. So, it's not 100% watertight, but a little di-electric on it before inserting the pin and I'm good with it.